Arena Reduces Prototyping Cycle by 70%
See how combining SOLIDWORKS software and 3DEXPERIENCE Works enabled Arena to reduce prototyping cycles, increase quality, automate workflows, and streamline collaboration.
Challenge
Reduce the time spent preparing prototypes of new swimwear and related products, and shorten the life cycle for producing new product prototypes.
Solution
Add 3DEXPERIENCE® Works collaboration tools to ensure all its designers have up-to-date feedback to create, test, and optimize models in real time. Arena also added 3D Sculptor and 3D Pattern Shape Creator, and reduced its prototyping cycle by 70 percent while decreasing time to market and enhancing quality by reducing the number of product defects.
Results
- Reduces Prototyping Cycle 70%
- Ensured all designers have up-to-date feedback to create, test, and optimize models in real time
- Reduced product defects
- Decreased time to market
Founder of Arena and son of Adidas founder Horst Dassler was on the pool deck at the 1972 Munich Olympics to witness Mark Spitz win his historic seven gold medals while setting seven new world records. Dassler immediately started forming plans for a swimwear company dedicated to aquatic sports and performance swimwear.
In 1973, just one year after the Games, Arena launched Skinfit® as its first competition swimwear line. The new ultra-light fabric only weighed 18 grams and was designed to cling to a swimmer’s body like a second skin.
Today Arena is headquartered in Tolentino, in central Italy, and is still fully dedicated to producing premium swimwear, equipment, and accessories for swimmers.
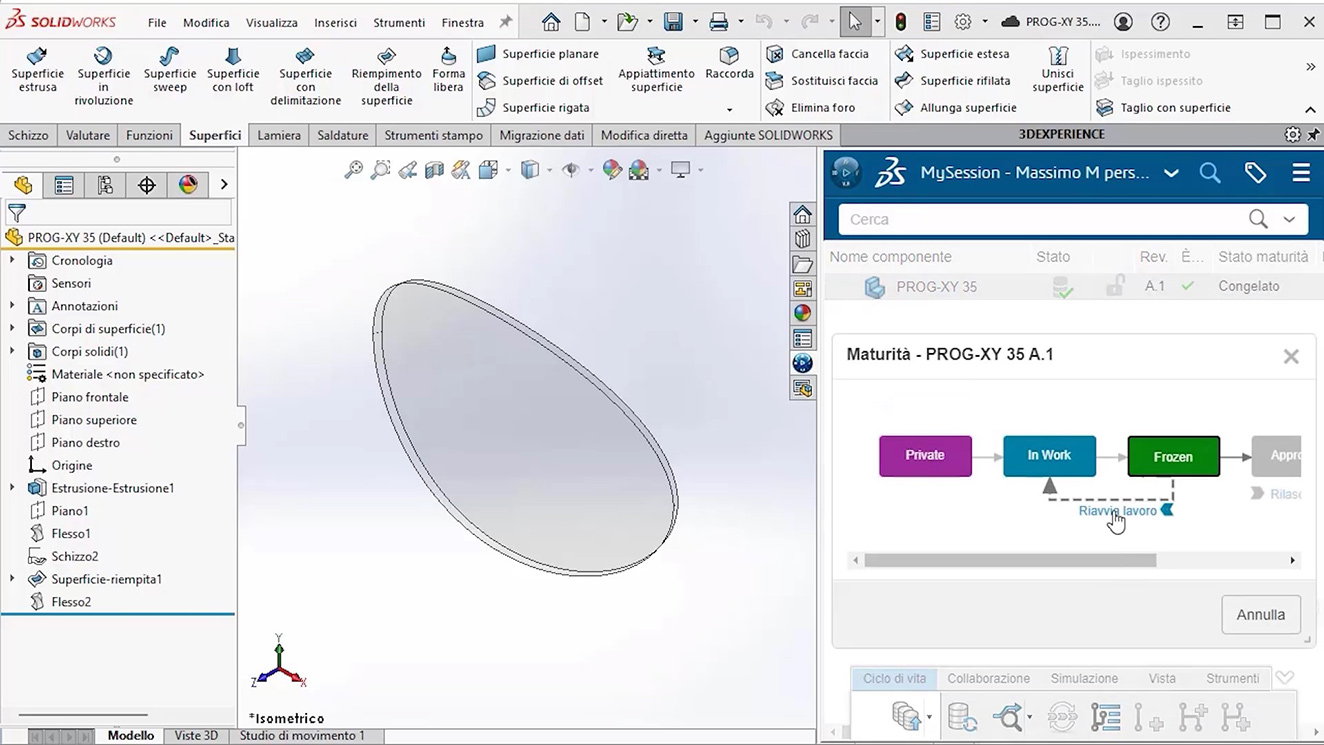
3DEXPERIENCE is helping us create an ecosystem, connecting all the necessary people with our designers.
Reducing Prototype Cycles
Arena Chief Information Officer, Andrea Mazzanti, knew the company needed to reduce the time spent preparing prototypes of new swimwear and related products. He also wanted to reduce the company’s carbon emissions. By moving to a 3D printing model, the company shortened the life cycle for producing new product prototypes. Arena also added 3DEXPERIENCE® Works to ensure all its designers have up-to-date feedback to create, test, and optimize models in real time.
Mazzanti explains, “3DEXPERIENCE is helping us create an ecosystem, connecting all the necessary people with our designers.” Arena mainly uses 3DEXPERIENCE with SOLIDWORKS® and 3D Sculptor, along with Simulation. With 3DEXPERIENCE Works, the company reduced its prototyping cycle by 70 percent while decreasing time to market and enhancing quality by reducing the number of product defects.
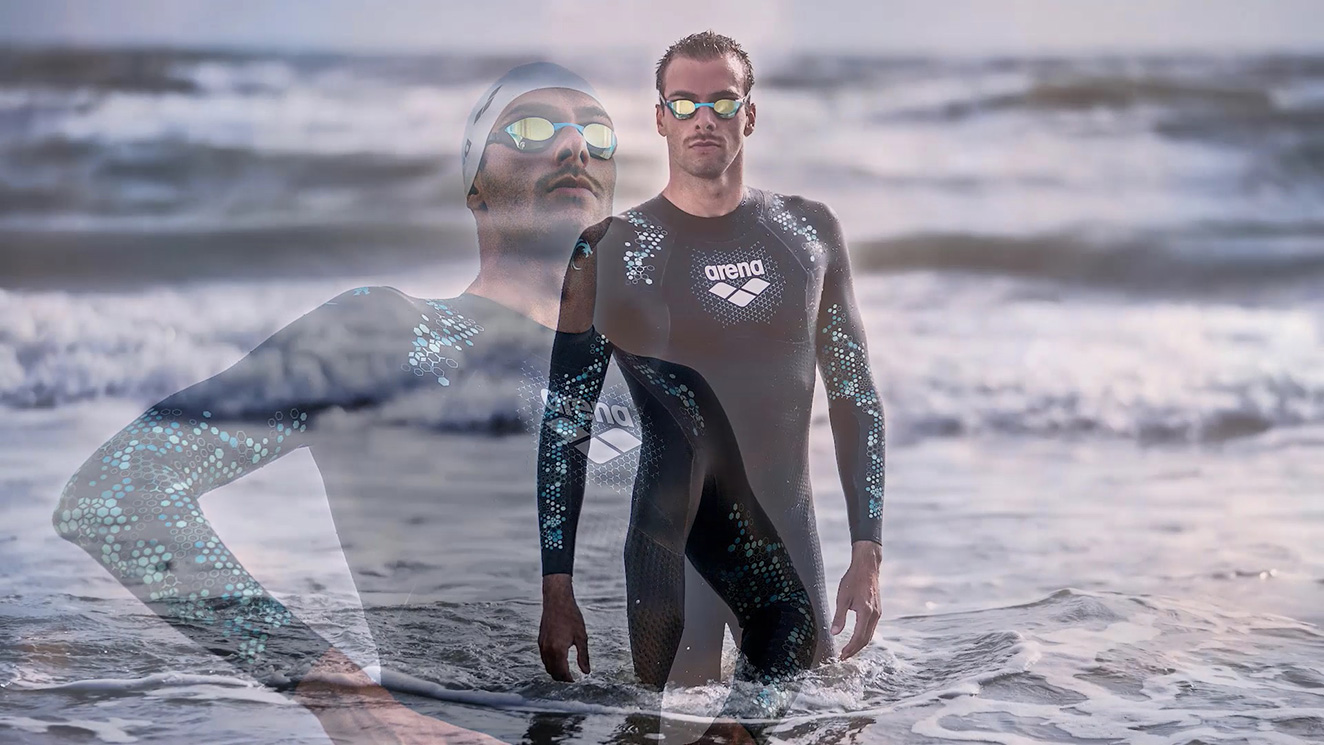
Related Resources
Leveraging Simulation to Preserve Resources
Another welcome benefit of decreasing the prototype cycle is the increase in sustainability from reduced carbon emissions. Mazzanti continues, “By simulating everything in our design office, we don’t have to create multiple product samples or use third-party product samples, so we reduce our CO2 emissions.”
Mazzanti predicts that digital technologies will continue to help Arena improve products for swimmers, particularly in capturing images and measuring and tracking data regarding the performance of fabrics on swimmers in the water. Technology can also help designers develop and test smart fibers.
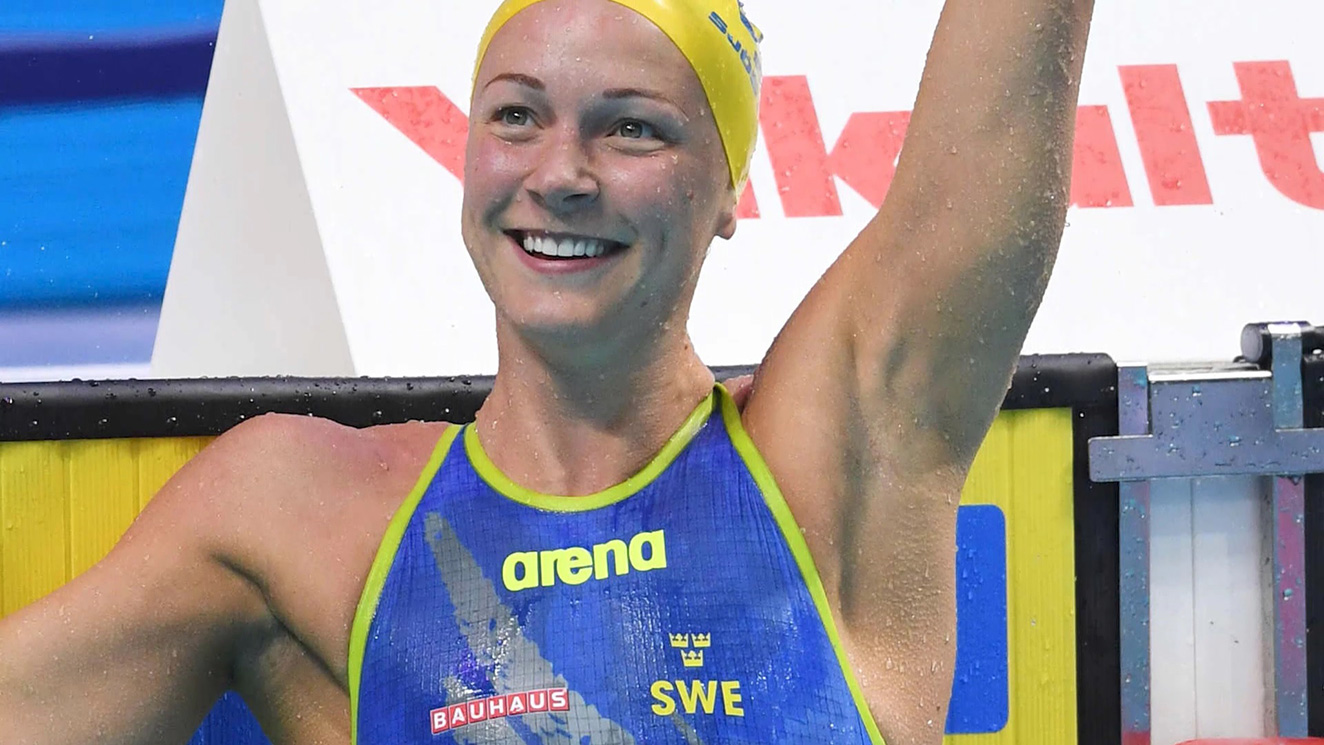
Game-changing Collaboration
Before 3DEXPERIENCE, the company’s workflow was messier – less predictable and more manual, and they often transferred data via Excel spreadsheets. Mazzanti concludes, “With 3DEXPERIENCE, we are in a single environment where designers can work together and quickly exchange information, which also greatly helps them collaborate with our partners.”
Local Italian reseller, Nuovamacut, helped Arena onboard 3DEXPERIENCE, SOLIDWORKS, 3D Sculptor, and Simulation and deployed the software to help design, measure, and test everything the company adopts. The collaboration was most productive, and Mazzanti looks forward to working with them in the future.
Learn More About 3DEXPERIENCE Works and SOLIDWORKS
Have questions about SOLIDWORKS and 3DEXPERIENCE Works Solutions?
SOLIDWORKS and 3DEXPERIENCE Works solutions enable you and your team to quickly transform new ideas into great products.