Dolphin Labs Converts Wave Energy into Power
SOLIDWORKS 3D CAD helps develop a rugged self-sustaining platform that turns ocean waves into a sustainable power source for critical marine data operations.
Challenge
Develop a complex system to convert ocean wave energy into an eco-friendly source of electricity. This system would harness the energy of ocean swells to power advanced data collection.
Solutions
Implement 3DEXPERIENCE Works design, modeling, collaboration, communication, and data management solutions in concert with SOLIDWORKS Standard design and Simulation Professional software.
Results
- Streamlined the design process by removing tedious bottlenecks Saved time and money during drone development
- Take away pain points in design to focus on important design challenges
- Managed data and version control transparently
- Avoided investments in costly IT infrastructure
Dolphin Labs is converting ocean wave energy into an eco-friendly source of electricity. The California-based startup is developing the xNode Wave Energy Converter, a remote sensing platform that harnesses the energy of ocean swells to power advanced data collection.
“Scientists have been trying to do wave energy conversion for at least the past 30 years, but there's some efficiency problems that haven't been solved yet,” explains Dolphin Labs Chief Engineer Chris Rauch. “One of the challenges with a wave energy converter is operating in an environment that can have 3 to 7 million cycles per year.”
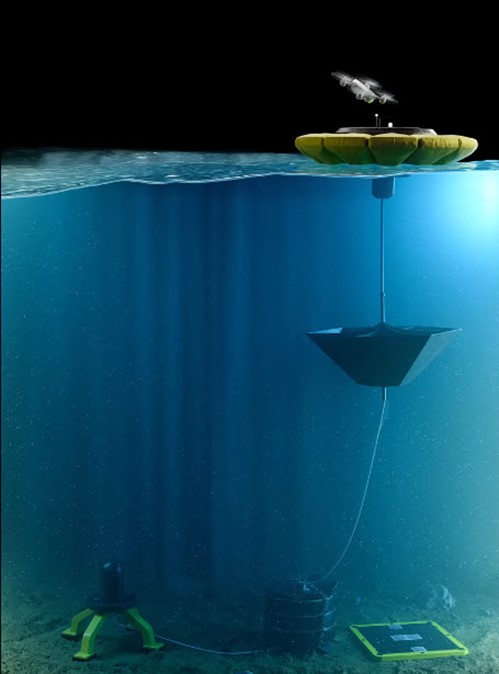
That means design durability is a top priority. Dolphin Labs addresses durability with the capacity to operate both submerged and on the ocean’s surface. “As the waves get bigger, we submerge deeper,” notes Rauch. That adaptability is key: Instead of bracing for catastrophic wave events like a 100-year storm, the platform can dive below the severe weather. Its lightweight and incidentally low-cost hull is also designed to withstand vessel strikes and other extreme conditions.
Charting a Better Course for Remote Sensing Platforms
The xNode Wave Energy Converter platform isn’t just a generator, it’s a self-sufficient wave-powered sensing system that leverages intelligence on the open ocean. Many existing systems are solar or wind powered, but the sun and wind are inconsistent and produce limited output. Dolphin Labs is charting a new course. Wave motion is a renewable energy source with more energy density than either solar or wind. That means xNode can support larger, more power-hungry sensors in offshore locations where they can be operated for extended periods of time.
SOLIDWORKS takes away pain points in design to let me focus on the really challenging parts of the problem.
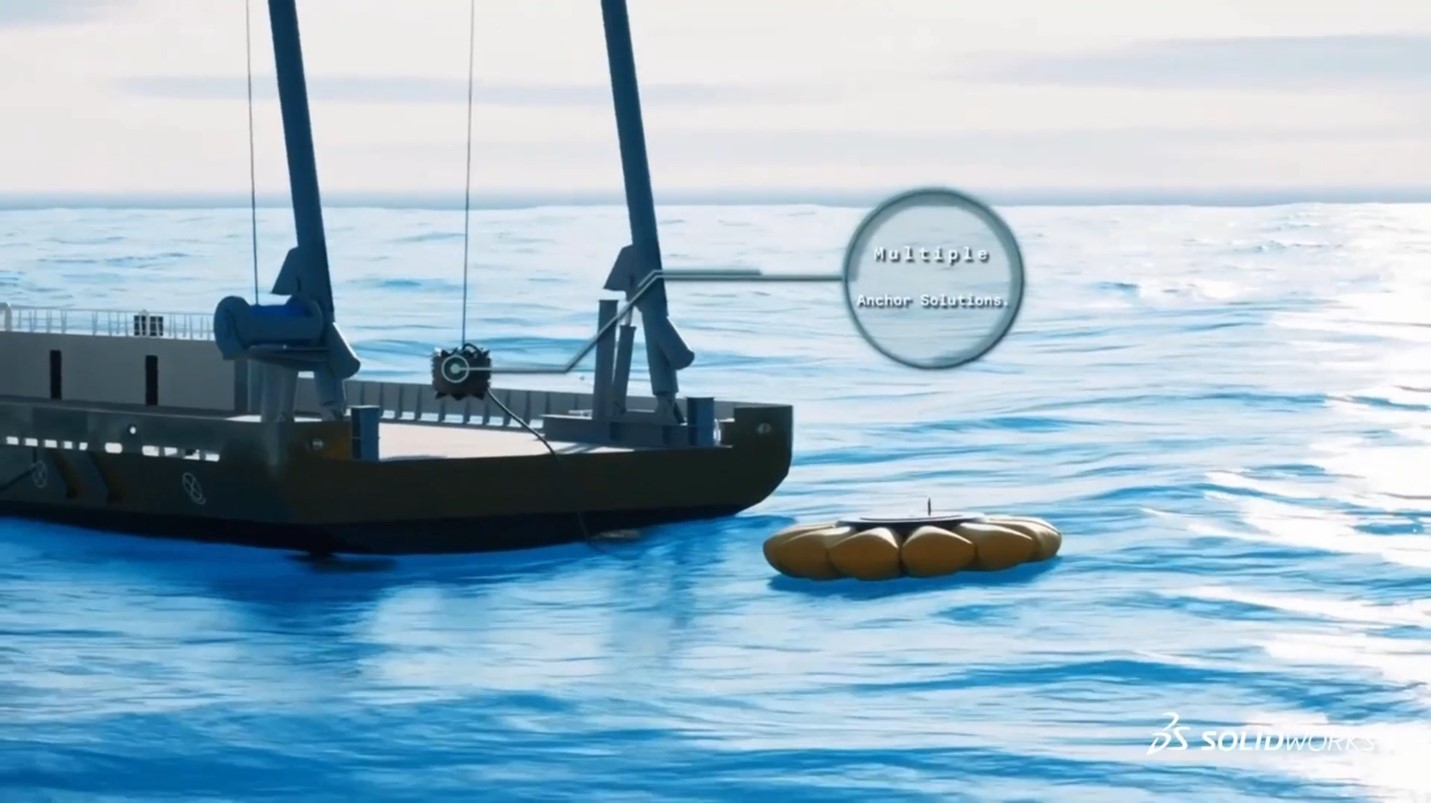
However, marine environments have myriad challenges. “Maintaining the reliability of technology in the ocean is tough,” observes Rauch. “It's hard to keep things working. And anything you put in the ocean—it really can't be a permanent system—whether you're dealing with galvanic corrosion or biofouling.”
Galvanic corrosion occurs when two dissimilar metals are electrically connected in a conductive environment, such as seawater. The more reactive metal (anode) corrodes faster than it would alone, while the less reactive metal (cathode) is protected from corrosion. Biofouling refers to the accumulation over time of biological organisms, such as algae, barnacles, and bacteria on surfaces submerged in water. This buildup can impair the performance of marine equipment, sensors, and vessels by increasing drag or blocking sensors.
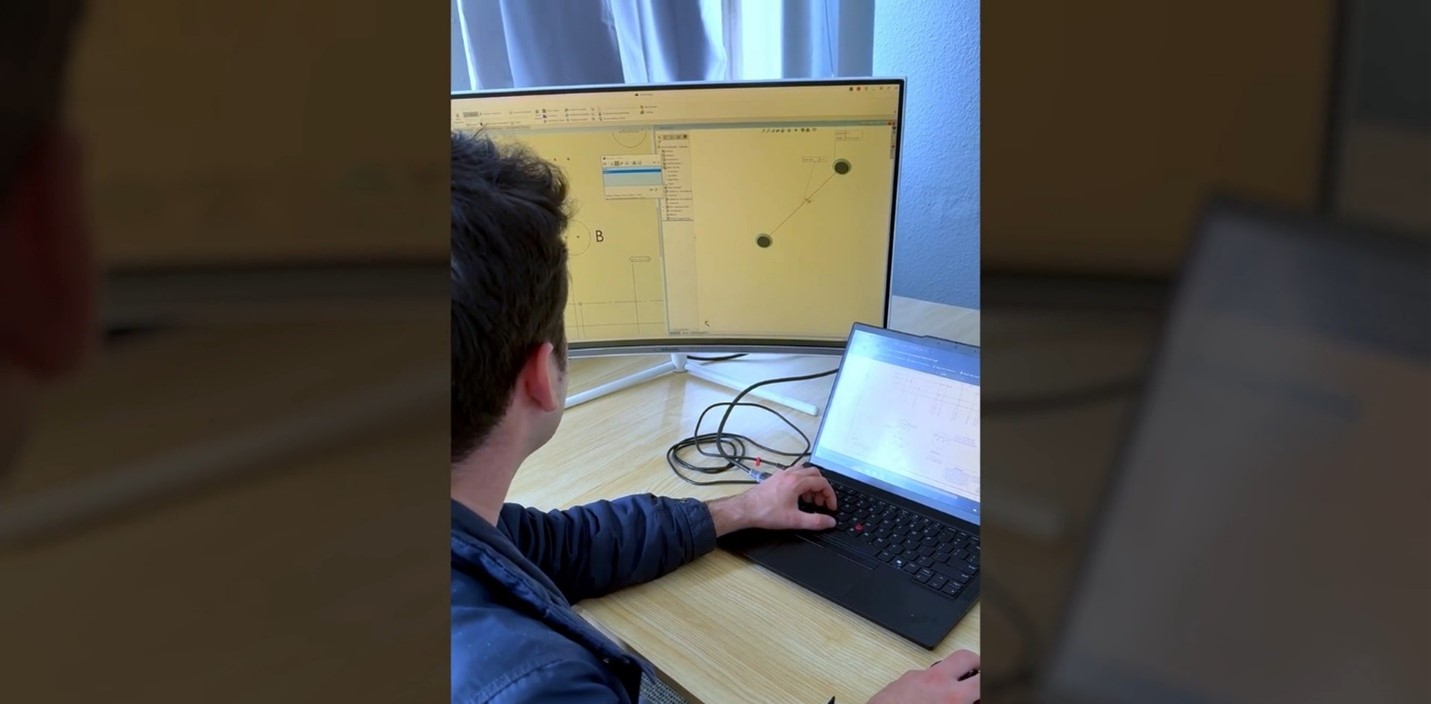
Designing Smarter Sensing Systems
Rauch has been using Dassault Systèmes SOLIDWORKS® for over two decades, starting right out of college when he was responsible for modeling hydrofoils for marine applications. SOLIDWORKS streamlined the design process by removing tedious bottlenecks, enabling him to dedicate more time to high-value engineering tasks such as simulation. “SOLIDWORKS takes away pain points in design to let me focus on the really challenging parts of the problem,” he adds.
Dolphin Labs integrates AI with edge computing to enable real-time data processing locally on its wave-powered buoys. Instead of transmitting massive datasets to the cloud, onboard AI models analyze sensor inputs locally, detecting critical issues and sending back only high-value insights. This approach reduces bandwidth usage, conserves power, and accelerates decision-making for Dolphin Labs customers.
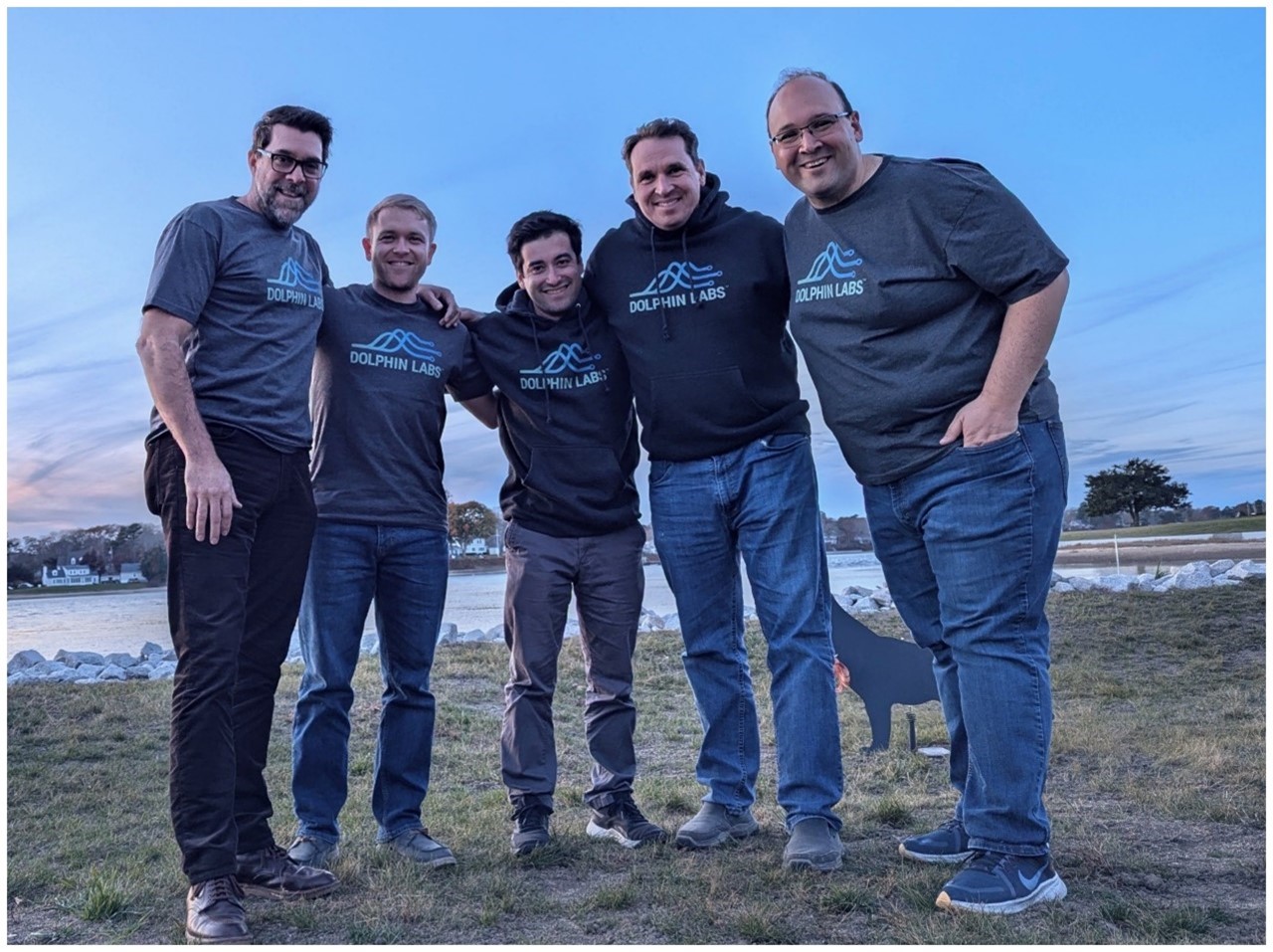
This added efficiency enables smarter ocean observation. Onboard the converter is a baseline suite of scientific sensors that’s fully compatible with third-party payloads. From fish stock monitoring to CO₂ measurements to acoustic tracking of marine mammals, the xNode adapts to any task.
The technology is also built to be sensor-agnostic, since every user has different needs. “We can incorporate whatever sensors are needed for a mission,” emphasizes Rauch.
On Track for Ocean Deployment
Currently the Dolphin Labs team is deep in prototyping. They’re ordering hardware, setting up test infrastructure, and finalizing structural designs with the goal of getting the first xNode in the water by Q3 2025.
Products:
- SOLIDWORKS Standard
- SOLIDWORKS Simulation Professional
- Collaborative Designer for SOLIDWORKS
- Collaborative Industry Innovator
- 3DSwymer
Learn More About SOLIDWORKS and 3DEXPERIENCE Works
Have questions about SOLIDWORKS Solutions?
SOLIDWORKS solutions enable you and your team to quickly transform new ideas into great products.