インドは世界第5位の鉄鉱石の埋蔵量を誇り、グローバルな鉄鋼業界の上位に名を連ねています。インドの仕上げ鋼の消費量は2億3,000万トンまで増加すると予想され、製鋼処理のイノベーションに拍車がかかっています。製鋼処理がうまくいくかどうかは、製造に回す鉄鋼を冷間圧延機で理想の形に成形できるかどうかにかかっています。
インドのファリダバド(デリーの真南)を本拠地とする大手平板処理装置メーカーのYogiji Digi社は、持続可能なイノベーションでエネルギーを節約しています。たとえば、同社の冷間圧延機の設計により、圧延荷重の消費エネルギーが2~3%減少しました。さらに、CO2排出量も年間356トン減少しています。
「私たちは、常に省エネと環境への影響を重視して装置を開発しています」とマネージングディレクターのNavneet Gill氏は語ります。「ほとんどの圧延機は、処理過程の中で大量の水を消費します。私たちは、他社製品より水の消費量が少ない圧延機を開発しました。その結果、圧延機1台ごとに、毎年約320万リットル(約845,350ガロン)の水を節約できます」
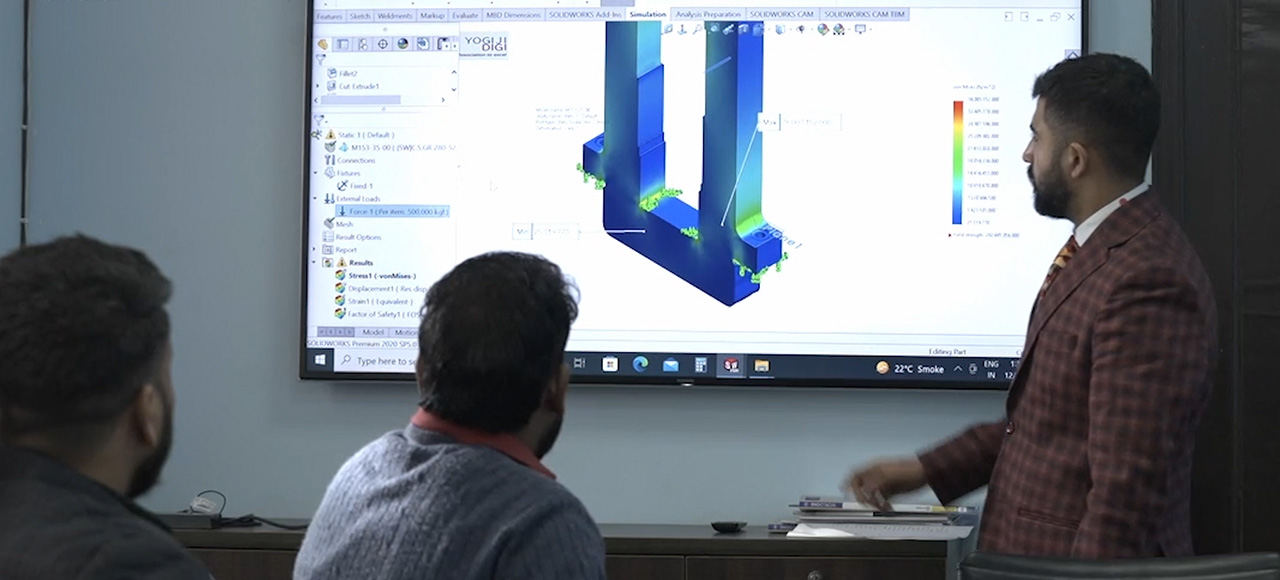
産業機械設計を最適化
Yogiji Digi社が直面している最大の課題は、圧延装置自体の巨大さと複雑さです。「装置をゼロから開発しようとすると、とてつもない時間がかかります」とNavneet氏は説明します。「私たちは、この課題をSOLIDWORKS Simulationプラットフォームで克服できました。
高速圧延設計には、ミクロン単位の精度と緻密さが求められます。「誤差を許容する余地はありません」と製品管理責任者のAseem Gill氏は言います。「完璧な設計が必要なのです」。サイズが大きくなるという理由だけで、ほとんどの産業機械には膨大な数の機械部品や電気部品が搭載されています。「SOLIDWORKSのおかげで、こうした作業がかなり楽になりました」とAseem氏は強調します。「部品表の生成には2日は必要でしたが、SOLIDWORKSなら、2時間しかかかりません」
Yogiji Digi社は、SOLIDWORKSで巨大な機械の設計も改善しています。「私たちは、ある顧客の粉砕ハウジングと冷間圧延機のアセンブリ一式を設計しました」と最高執行責任者のVarun Rana氏は説明します。「最終的に、粉砕ハウジングの重量を最大30%削減できました」
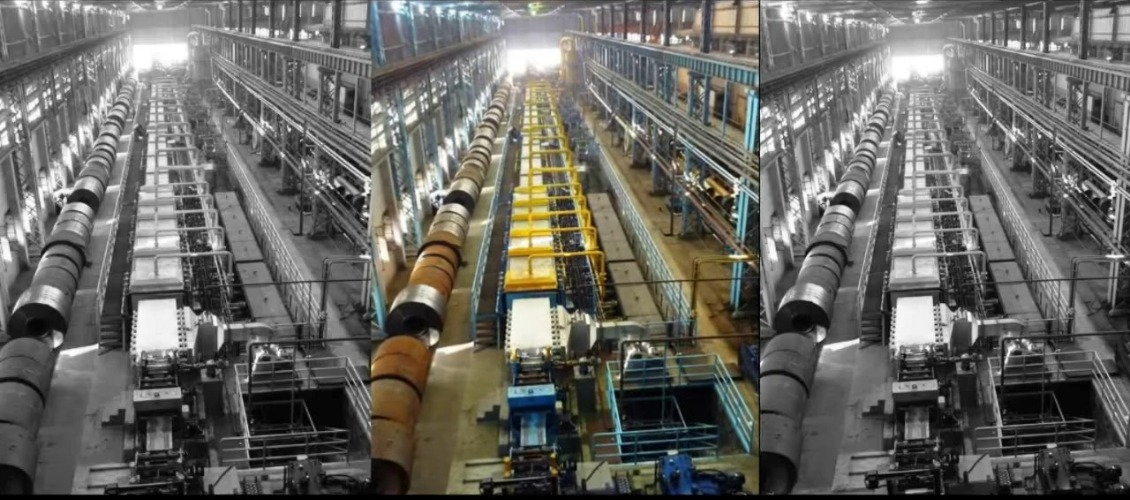