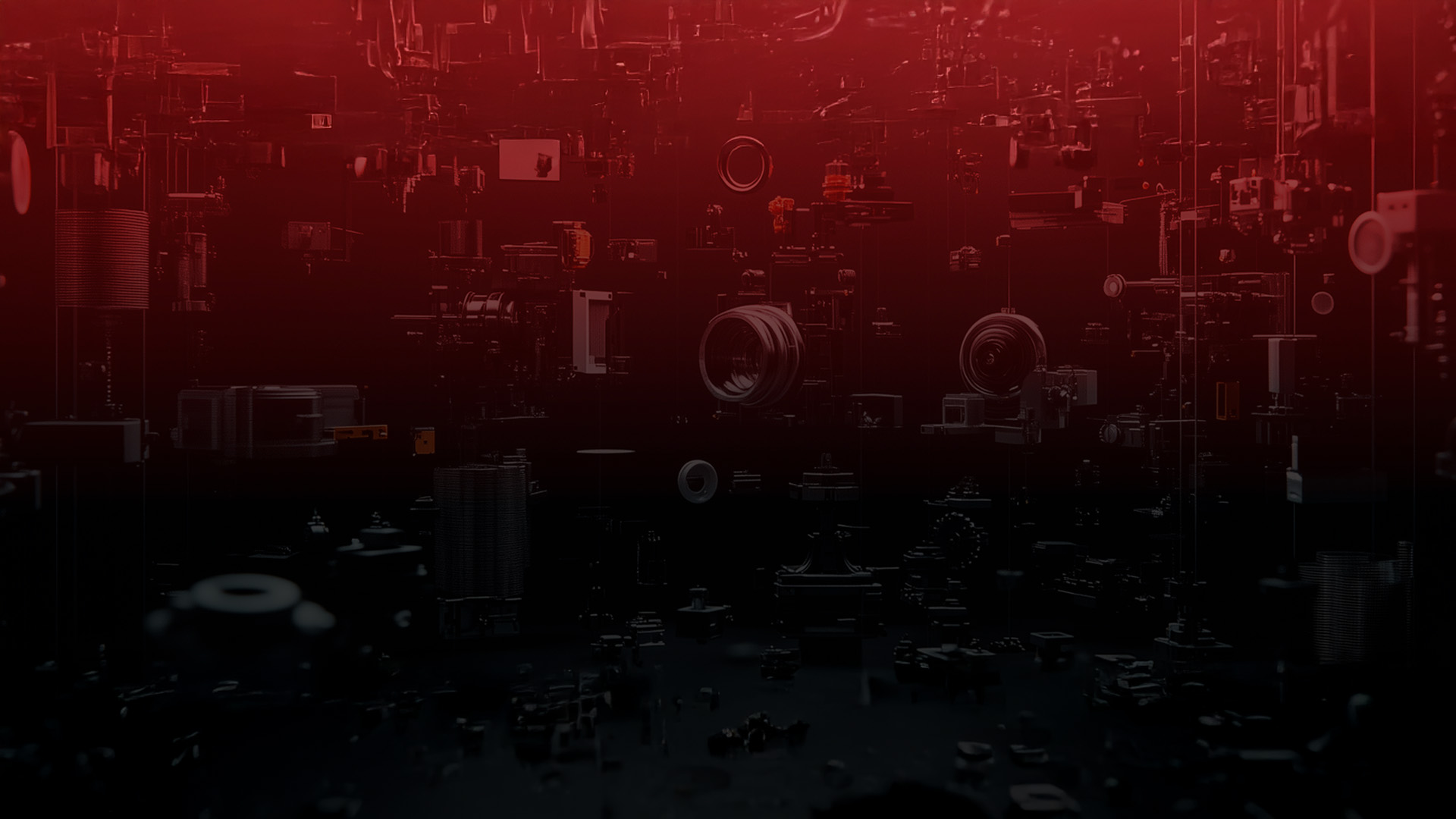
Know Your Designs Will Pass the Injection-molding Process
Producing high-quality, plastic injection-molded parts more quickly and cost-effectively than the competition has become a critical factor for manufacturing success in today’s global market. However, producing injection-molded parts that are free of manufacturing defects requires a complex mix of time, temperature, pressure, material, and variations in tooling or part design.
Don’t cave to complexity. Read this white paper to learn how designers, moldmakers and manufacturers are saving time and money by answering these questions with SOLIDWORKS® Plastics before cutting steel:
- Does the part geometry meet draft and wall thickness requirements?
- How long should the injection/cooling/ejection cycle be? What’s the optimal temperature for the material, cooling channels, and mold?
- What’s the right filling/packing pressure and best material to use for a particular part?
- And, will the use of special inserts, side actions, additional injection gates, special secondary operations, or unique cooling channel designs improve part quality or shorten cycle times?