Competing on Quality & Agility in the Medical, Healthcare and Pharma Industries
By harnessing data in the DELMIAWorks (formerly IQMS) manufacturing ERP system, COMAR LLC has the real-time insights to drive innovation, ensure the quality that differentiates it from competitors, and enable the agility to address customers’ demands.
The Need
By standardizing on the DELMIAWorks manufacturing ERP system across all of these facilities, Comar has been able to accelerate its new product development and introduction process while also staying agile enough to take on custom product orders.
The Solution
Outfitted with sensors, the machines on Comar’s shop floors complement DELMIAWorks’ real-time monitoring functionality to provide the manufacturing intelligence managers need for making timely, informed decisions.
The Results
- Real-time data dashboards with insights into production efficiency and quality
- Agility to adapt to customers’ short-notice production runs
- Streamlined customer audits
- Greater financial visibility and control
- Access to data that results in faster decision-making
- Reduce downtime and preventable breakdowns
Investing in Software and Machinery to Drive Agility
Headquartered in Voorhees, NJ, Comar has grown from two manufacturing locations to nine facilities across the United States and Puerto Rico, staffed by more than 900 employees. By standardizing on the DELMIAWorks manufacturing ERP system across all of these facilities, Comar has been able to accelerate its new product development and introduction process while also staying agile enough to take on custom product orders. “The modularity and scalability of our DELMIAWorks ERP system has provided us access to data that results in faster decision-making, in spite of the fact that we have a more complex business,” observes Tom Sine, Comar business systems manager.
We can look at the same thing in nine different plants, assess performance, and make business decisions quickly. Our customers definitely value this speed and agility
Analytics and data-driven approach to evaluating potential acquisitions
The company also relies on the ERP system to support its analytics and data-driven approach to evaluating potential acquisitions. And although DELMIAWorks expertise is not a key requirement for acquisition, Comar has found that it can often get an acquired plant up and running within six to nine months when DELMIAWorks is already in use there.
In addition to its manufacturing ERP software, Comar has also brought on new machinery to increase its ability to adapt to customers’ short-notice and often highly customized production runs.
“We’re investing in machinery that can handle faster change-overs for short-notice production runs and will support faster production runs overall,” explains Scott Conklin, Comar executive vice president of sales and marketing.
Real-Time Monitoring For Faster Decision-Making
Outfitted with sensors, the machines on Comar’s shop floors complement DELMIAWorks’ real-time monitoring functionality to provide the manufacturing intelligence managers need for making timely, informed decisions.
“We’re a metrics-driven organization and have robust business systems that provide us access to real-time web-based dashboards that are fully integrated with our DELMIAWorks ERP data,” Conklin explains. “The dashboards are refreshed every 15 minutes and can be set up to proactively alert decision-makers to recognize success—for example, a record day in production—or to bring attention to a mold, machine or process that isn’t performing to our expectations, so we can better manage our operations.”
Comar also relies heavily on real-time monitoring to gain valuable insights into how every machine on each of its production centers is operating. By monitoring production variances, defects can be adjusted out to increase yield while decreasing waste.
“DELMIAWorks has a module for managing preventive maintenance,” notes Sine. “So, when a machine is running, the real-time production hours and cycles are counted. With this data, the system can trigger preventive maintenance work orders on machines as well as molds. This has been especially helpful in reducing downtime and preventable breakdowns to ensure we meet our customers’ requirements.”
With DELMIAWorks, Comar also has a standardized platform where all data is managed in one place. This has enabled the company to speed its decision-making, allow for better centralization, and optimize management oversight, leading to greater agility.
“With DELMIAWorks, we’ve been able to increase our adaptability to our customers’ needs for short-notice production runs,” Conklin observes.
We build quality into our process and measure key metrics to ensure reliability and consistency of results for every customer.
Competing on Quality
By taking a proactive approach to defect prevention and continuous improvement, Comar strives to achieve quality objectives for customer satisfaction, on-time delivery, and operating efficiency.
Comar’s reputation for quality has made the manufacturer a market leader in North America and a preferred solutions provider.
Managers at Comar believe that the more accurate, rigorous, and scalable their quality management systems are, the better they will be able to continually improve to meet customers’ changing product and business requirements. The company operates on its TPI-Three principles for total process improvement, which are grounded on the Six Sigma DMAIC-based (Define, Measure, Analyze, Improve, and Control) approach to ensuring product quality that the company adopted decades ago.
“Our TPI-Three journey grew out of our engineering-driven approach to quality, where we put the customer’s requirements at the center of every quality management process,” Conklin explained.“We build quality into our process and measure key metrics to ensure reliability and consistency of results for every customer.”
The DELMIAWorks ERP system supports these efforts by providing the quality management system (QMS) functionality essential for planning, executing and evaluating the success of every customer engagement, from first order through shipped products.
[When] a machine is running, the real time production hours and cycles are counted...This has been especially helpful in reducing downtime and preventable breakdowns to ensure we meet our customers’ requirements.
Investing in Quality Compliance and Certifications
Comar’s quality management practices are backed by extensive investments in meeting a range of quality and regulatory standards. All nine manufacturing plants are ISO-certified and provide ongoing quality data to centralized quality management teams to ensure corporate-wide quality goals are met and exceeded.
Comar also has achieved FDA medical device registration #2220100 in addition to ISO 9001 and ISO 13485 certifications, uniquely positioning them to provide medical plastics packaging customers with either standard or custom-designed packaging materials. Comar is finding the quality management and engineering expertise needed to maintain these certifications are exactly what new medical packaging customers are searching for in a supplier.
Additionally, Comar has achieved Current Good Manufacturing Practice (cGMP) compliance and offers expertise in low-particulate manufacturing capabilities, statistical process control (SPC), and state-of-the-art vision inspection. Comar products are listed in Type III drug master files, and various facilities comply with FDA drug master files, including DMF #16669, DMF #7844, DMF #16762, DMF #6609, and DMF #4671. The company also maintains device master files and device history files across all production centers, and it meets European Union requirements for CE mark certification for specific products.
The DELMIAWorks system provides us with an easily used document library and production data to handle customer requests and make audits efficient.
Traceability Helps Automate Customer Audits
Another dimension of quality is having the ability to track and document manufacturing materials, processes and production. Comar receives on average five audit requests per month from its customers, the majority of them in the healthcare and life sciences fields. Using the traceability functionality in the DELMIAWorks ERP system, Comar is able to automate much of the audit production.
“Being able to quickly point to and document how raw materials and other supplies make their way through our manufacturing operation into finished goods inventory and ultimately into finished goods arriving at our customers’ doors is a key traceability requirement,” notes Conklin.
In addition to the traceability capability, Sine explains that, “The DELMIAWorks system provides us with an easily used document library and production data to handle customer requests and make audits efficient.”
Comar also finds that the more regulated a customers’ industries are, the more thorough their audits tend to be. They want to know with precision about a resin lot in question, what day and time a part was produced, what employees were working, and what training those employees had. In addition, the company is seeing more requests from healthcare and medical products customers who want to see machinery performance data. Using the real-time data stored by the ERP system, Comar has the information to answer such questions.
“Customers have grown accustomed to viewing corrective action reports during their audits in the DELMIAWorks system,” Sine observes. “And, they appreciate and respect the fact that we’re using an established, well-known and trusted ERP system.”
Embracing Sustainability
In addition to driving manufacturing efficiencies through its data-driven approach, Comar is leading innovations in sustainable packaging initiatives. For example, the firm recently collaborated with equipment vendors to improve process control on innovating a new injection stretch blow molded bottle for gummy vitamins, and it has been able to reduce the amount of resin needed per bottle by up to 20% depending on the bottle size.
“Sustainability and ‘Reduce, Reuse, Recycle’ are core to many of our customers’ value propositions,” Conklin explains. “We are using insights from our DELMIAworks system to help introduce new products that support their initiatives.”
Conclusion
By harnessing data in the DELMIAWorks manufacturing ERP system, Comar has the real-time insights to drive innovation, ensure the quality that differentiates it from competitors, and enable the agility to address customers’ demands for short-notice production.
IQMS was acquired by Dassault Systèmes® and has been rebranded as DELMIAWorks, part of the 3DEXPERIENCE® Works design to manufacturing software portfolio for mid-market manufacturers.
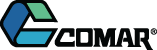
More on Comar
Comar (www.comar.com) is a fast-growing manufacturer of plastic packaging products and components for the medical, pharmaceutical, healthcare, personal and home care, food and beverage, and niche markets. Quality is a key priority for the products that the company produces, which include fully assembled medical devices, diagnostic consumables, and a broad line of stock and custom products, including oral dispensers, dosage cups and spoons, dropper assemblies, plastic bottles, wet wipe containers and lids, and closures.
DELMIAWorks Additional Resources
Resource Center
Access brochures, case studies, testimonial videos, whitepapers, eSeminars (Webinars On-Demand), and more.
DELMIAWorks User Community
Online community of DELMIAWorks users (3DEXPERIENCE Platform login credentials required)
Training & Services
Learn more about DELMIAWorks Software Training Programs and Solution Consulting Services.
Have questions about DELMIAWorks Manufacturing ERP Solutions?
DELMIAWorks solutions solve your manufacturing challenges by connecting the entire design to manufacture process.