What it takes to Win Plastic Processor of the Year
Partnership with IQMS — now DELMIAWorks — Strongly Supported the Growth and Performance Acknowledged in This Prestigious Award
The Need
The company invested in and implemented IQMS (now DELMIAWorks) enterprise resource planning (ERP) to upgrade from the combination of systems it had been using since its inception, but which no longer satisfied the needs of its ambitious growth goals.
The Solution
Dymotek partnered with IQMS, making a strategic decision to use the software to operate all aspects of its business. The integrated system gives them the flexibility to manage their business needs and provide real-time information to their customers, as well as delivers the agility necessary to adapt to changing demands in an increasingly challenging global marketplace.
The Results
- 111% growth in three years
- Automated tasks save users time—and saves the company money
- Optimized inventory management
- More efficient production scheduling
- improved efficiency, visibility, and productivity
- Customer service excellence
A combination of disparate systems no longer supported ambitious growth goals
In 2016, Plastics News awarded Ellington, CT-based Dymotek the Excellence in Customer Relations Award. In 2017, the company raised its game even higher, as the leading industry journal honored it with its Processor of the Year Award.
“Winning this award is a ‘bucket list’ item for me,” says Norm Forest, CEO of Dymotek. “It’s a very short list that competed for the honor—21 other great companies in our industry. To even be on the stage with that group is an honor, let alone to walk away with the award. It’s a humbling experience, and one that everyone at the company has worked very hard to achieve.”
Founded as Truebro, Inc., in 1990 by brothers Steve and Tom Trueb, the company has grown from a small family venture to one of the nation’s leading custom molders. Originally the company made a single product: an easily installed universal pipe cover called Lav Guard. It was the first product of its kind to meet a new set of regulations mandated first in Connecticut, then nationally, as part of the American Disability Act (ADA) requiring protective covering for pipes under sinks. Truebro set up a dedicated molding facility in 1997 to meet the growing demand as their product line developed. The original three-shift molding operation started with two machines.
As the company augmented its signature product line to sustain what was then a 24/5 operation, it added custom injection molding to its capabilities, which became the company’s core business. In 2004, the company sold it’s Truebro brand and product line to an organization that continued to contract with them for production, and formed Dymotek as a custom injection molder that specializes in liquid silicone rubber and multi-component molding. The infrastructure that was built over the company’s first decade became the base of an exciting new venture.
The year 2004 was a signature one for Dymotek. The company added 21,000 square feet of production space; 10,000 square feet was dedicated to manufacturing and 11,000 sf warehouse. (It was in 2015 that we built out a new molding facility at a rental property adding 48,000 sf). That same year the company invested in and implemented IQMS enterprise resource planning (ERP) to upgrade from the combination of systems it had been using since its inception, but which no longer satisfied the needs of its ambitious growth goals.
A Foundation for Growth and Change
Dymotek partnered with IQMS, making a strategic decision to use the software to operate all aspects of its business. The integrated system gives them the flexibility to manage their business needs and provide real-time information to their customers, as well as delivers the agility necessary to adapt to changing demands in an increasingly challenging global marketplace.
“Prior to this implementation, we managed and scheduled using Excel and other products; having one completely connected ERP system is far superior to our legacy arrangement,” notes Forest. “I no longer have to rely on three or four canned systems without common terminology communicating with each other; everything is connected seamlessly in a one-stop solution with IQMS.”
That capability proved itself almost immediately. Because of the sale of Truebro and its product line, it was imperative to split those assets from the rest of the company holdings. “It would have been incredibly difficult to go through the sale with our earlier systems; but because of IQMS, we were able to separate things out easily,” explains Forest.
As Dymotek continued to build and grow its business, another aspect of IQMS proved vital: having an exact understanding of the costs of goods produced. With IQMS, Dymotek could quickly and precisely assess the cost and profitability of any item they sold. This included the cost of equipment usage involved in production, which the system delivered in real time.
What’s more, the visibility and communication enabled by IQMS gave Dymotek the ability to provide that excellence in customer service. “For example, we had a customer that wanted to know exactly what was on our production floor daily because they had tight requirements for inventory,” recounts Forest. “They wanted to know specifically what was produced, what was on the schedule, what was in quarantine, and so forth. With IQMS, every morning we sent an e-mail that gave them the complete reconciliation of all the products we had in house, so that they could plan their commitments for their customers accordingly. That kind of power is vital, and has really supported our success.”
Other IQMS tools Forest calls out as important:
- IQAlerts. The IQAlert module automates routine tasks and turns static data into active system notifications. Automated tasks save users time—and saves the company money—while instinctively tracking data to prevent key company developments from slipping through the cracks. As Forest says, “Now we push information out instead of having to pull it in.”
- Engineering Change Orders (ECO). The ECO module provides a centralized location to control item revisions, bill of material changes, and more. E-mail notifications are sent through a web-based approval process to the individuals responsible for each step, requiring review and/or approval, and facilitating the exchange of ideas. “With ECO, it’s easy to communicate changes without tying personnel up in meetings,” says Forest.
- Real-Time Production Monitoring. IQMS’ Real-Time Production Monitoring supports machine management in true real time. All aspects of production are tracked immediately as parts are being made and applied to the shop orders, automatically updating the schedule and finished product counts. The results of this embedded solution are improved efficiency, visibility, and productivity. “With this capability, our supervisors can see at a glance where support is needed,” notes Forest.
Prize-Winning Performance and 111% Growth
When asked if Dymotek would have won the Processor of the Year Award without having IQMS in place of its former systems, Forest’s response is adamant: “No way! We never would have experienced the growth. We grew 111 percent in three years. Without IQMS, there is no way that we could have delivered on that much new business. We actually grew 62 percent in one year, with a highly complex launch of three different machines, and with an intense level of training. We went from about 50 people to 100; not only did we pull it off, but at the end of the year, a major OEM gave us an award for service excellence.”
According to Forest, IQMS was a major key factor in this success. The system keeps them disciplined. They must play by rules that keep them executing at a high level.
Among the modules Forest cites as strongly supporting Dymotek in the award competition are Asset Management and Training. Asset Management supports on-time delivery. Dymotek’s molds are in that module, which means that preventive maintenance is occurring on the molds, eliminating the run-to-failure-type scenarios that cause a host of problems. The training module allows Dymotek to see their personnel skillsets and determine what specific training is needed as well as if individuals are capable of running authorized processes.
“The whole system provides a foundation of support that lets us efficiently and effectively execute the outputs we need, which are best-in-class,” says Forest. “A lot of what IQMS does is ‘behind the scenes’ work; the system is intertwined with every aspect of the business.”
Strong Support from the Get-Go
Forest describes the IQMS company as a “complete partner” from day one. “We’ve never had a problem with support,” he remarks. “If I have an issue and need it corrected, I need to know I’m not at the end of a list of 100. IQMS has always been very responsive to our needs.”
In particular, Forest has found that leveraging IQMS’ Professional Services group has been extremely beneficial. Previously the company had a master scheduler where people would pick and choose to complete the schedule; however, Professional Services came in and showed a better way to schedule. Additionally, the company wasn’t processing fixed and standard costs in a manner that optimized inventory management. Again, IQMS was called in to remedy the situation. In both instances, an IQMS Professional Services consultant spent a day or two at Dymotek working with the company to analyze the situation, then provided a solution for better, more robust performance.
“Typically the consultant went away for a few months, and when they’d return everything was working great,” says Forest. “That was because they left us with a lot of assignments; completing those tasks instilled the discipline to do things the right way.”
For all the benefits Dymotek has garnered through its use of IQMS, Forest believes the best is still to come. “As we get better and more confident in using the services IQMS provides, we continually find other things that we could be doing,” he concludes. “We just keep peeling back the onion to reveal new layers, and that’s exciting. It’s a very powerful system, but you need to be smart about your approach and leverage the resources you have at hand.”
That’s what Dymotek plans to do. If the assessment of their industry peers is any indication, you can be sure that they will.
IQMS was acquired by Dassault Systèmes® and has been rebranded as DELMIAWorks, part of the 3DEXPERIENCE® Works design to manufacturing software portfolio for mid-market manufacturers.
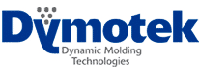
More on Dymotek
Originally established in 1990 as TRUEBRO, Dymotek has a track record for designing, molding, and bringing to market innovative, proprietary products. Many of which have become respected and preferred mainstays within the industries they target.
DELMIAWorks Additional Resources
Resource Center
Access brochures, case studies, testimonial videos, whitepapers, eSeminars (Webinars On-Demand), and more.
DELMIAWorks User Community
Online community of DELMIAWorks users (3DEXPERIENCE Platform login credentials required)
Training & Services
Learn more about DELMIAWorks Software Training Programs and Solution Consulting Services.
Have questions about DELMIAWorks Manufacturing ERP Solutions?
DELMIAWorks solutions solve your manufacturing challenges by connecting the entire design to manufacture process.