SIGN Fracture Care International: Operating at the Highest Level of Efficiency
Non-profit optimizes the production of devices for healing bone fractures in disadvantaged communities with DELMIAWorks and SOLIDWORKS
Challenge
Maximize efficiency in designing and producing medical instruments and implants for disadvantaged communities while streamlining International Standard Organization (ISO) and Food and Drug Administration (FDA) compliance—within a budget based 100% on donations.
Solution
Implement two key Dassault Systèmes products to automate the non-profit’s design and manufacturing operations: SOLIDWORKS 3D design software and the DELMIAWorks manufacturing enterprise resource planning (ERP) system.
Results:
- Saves 20-plus hours per week by reducing errors and streamlining production checks
- Simplifies development of medical devices for resource-constrained settings
- Streamlines ISO 13485 and FDA regulatory compliance
More than half of the world lives on less than $5.50 per day. So, when a person living in a low- or middle-income country breaks an arm or leg, it can easily send their whole family spiraling into poverty. SIGN Fracture Care International, a non-profit humanitarian non-governmental organization (NGO), enables a patient with a fractured bone to stand in one day, leave the treatment center in one week, and be back at work or school in one month.
SIGN: Committed to Rebuilding Patients’ Lives
SIGN manufactures low-cost surgical instruments and implants to stabilize fractured bones. These devices can be used in the most basic treatment settings, even those without x-ray machines or electrical power, and the organization delivers them to remote regions with precision and timeliness. Not only does SIGN donate the instruments and implements; it also donates training and education to empower doctors in the communities they serve. By working with teaching hospitals and hosting educational conferences worldwide, SIGN equips surgeons to heal patients within their own local communities.
As a humanitarian organization, return on investment at SIGN is not calculated in dollars but rather in the number of patients whose quality of life and productivity have been restored after a serious injury. To date, SIGN has teamed with surgeons to heal more than 450,000 patients in 60 countries.
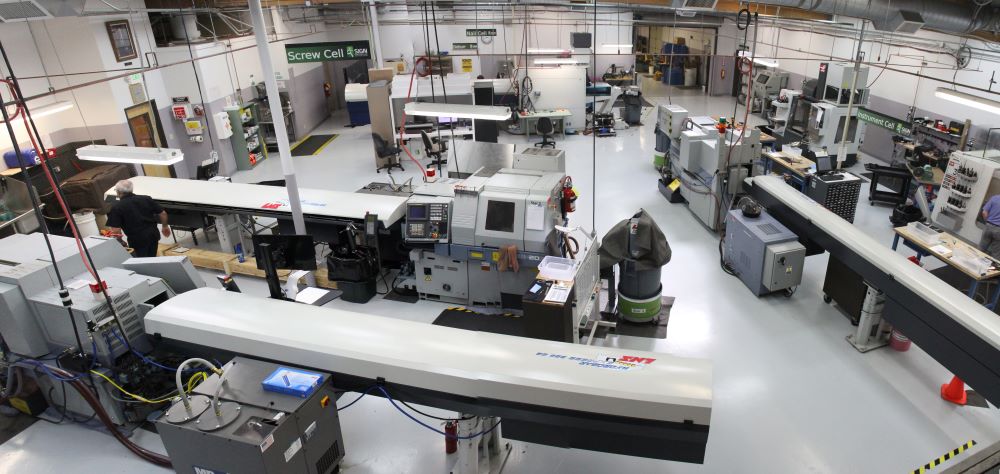
Because SIGN relies 100% on donations from private donors, organizations and foundations, it needs to operate at the highest level of efficiency and produce the most instruments and implants possible with the available funding. To support its design and manufacturing operations in achieving this objective, SIGN relies on two key products from Dassault Systèmes: SOLIDWORKS 3D design software and the DELMIAWorks manufacturing ERP system.
Creating Innovative Medical Device Designs with SOLIDWORKS
Since 2001, SIGN has relied on SOLIDWORKS to design both its surgical instruments and implants, guiding them from conceptualization through creation, validation, and delivery to patients via their network of orthopedic surgeons.
Terry Smith, engineering manager at SIGN, emphasizes that since the early days, SolidWorks has been integral to the non-profit’s product design process, noting, "Without it, we wouldn’t be where we are today."
The software enables SIGN to import and model anatomy, design implants, and surgical instruments crucial for treating injured patients in need. SIGN has utilized SolidWorks' capabilities to innovate and develop products suitable for resource-constrained settings, empowering surgeons to effectively treat orthopedic trauma patients. This includes conducting finite element analysis (FEA) simulations, rendering models for surgical technique manuals, and utilizing its product data management (PDM) system for managing change control within a regulated environment.
We use the DELMIAWorks quality modules to trigger and document all of our in-process and final inspections as well to schedule and document all of our gauge calibrations. The savings have been tremendous.
Ensuring Manufacturing Quality and Compliance with DELMIAWorks
In 2023, SIGN implemented Dassault Systèmes’ DELMIAWorks ERP system to manage its manufacturing processes, which has enabled the non-profit to move to paperless manufacturing workflows and quality control.
“We have transitioned from paper-based manufacturing processes to paperless processes. For instance, previously our job travelers were actual paper folders of documents, whereas now they are digital documents accessible to all staff and operators. At the work centers, our operators work in front of two screens: one showing the device drawing and the other the inspection requirements. They no longer have to shuffle through folders to get the most current information and specifications,” says Bob Schmitt, manager of regulatory affairs at SIGN.
Schmitt adds, “The same can be said of our inspection records. Now, in-process and final inspections are digitally recorded in the Quick Inspections module along with the calibrated inspection instruments used to accept product. ISO 13485 and FDA auditors now prefer evidence-based audits over the older narrative-based format, so having ready access to comprehensive device history records is critical in demonstrating regulatory compliance. The DELMIAWorks Assembly Lot History report and the Inspection Sample Log report together serve us well in capturing these highly regulated inspection results.”
As an FDA-registered and ISO 13485-certified medical device manufacturer, properly calibrated inspection equipment is fundamental to quality inspections. Therefore, rigorous calibration and documentation of inspection equipment are also essential.
“We use the DELMIAWorks quality modules to trigger and document all of our in-process and final inspections as well to schedule and document all of our gauge calibrations,” Schmitt explains. “Before we went digital, the inspection processes produced more paperwork, required more double checks, and used more storage and retention resources than perhaps any other processes in the business. Now, all that is done on the system, and all the storage is digital. The savings have been tremendous.”
Additionally, to ensure compliance with the FDA’s electronic signature regulations, SIGN uses the CRF Part 11 features of the DELMIAWorks system to require dual digital signature authentication. By automating this and other processes, the non-profit has gained significant efficiencies across the organization.
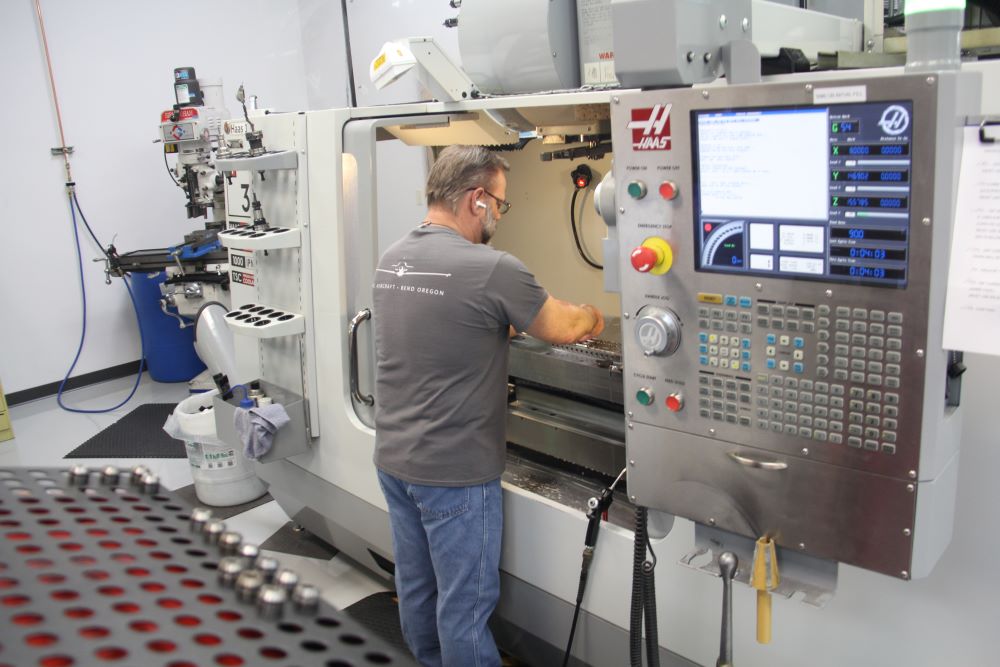
“Converting to digital data processes and controls is saving 20 or more hours a week by reduced errors and streamlining pre- and post-production checks,” observes Shelly Foster, logistics and operations analyst at SIGN. For example, she notes, “Saving 10 minutes each on 1,500 folders really adds up over time and lets me focus other aspects of my job.”
Both Schmitt and Foster agree: ERP promotes a consistency of workflows, and predictable, consistent workflows are the foundation of efficient production and quality assurance.
Delivering Results While Driving Inspiration
SIGN’s mission—and the commitment of the NGO’s founder and team in fulfilling it—is an inspiration to all who come in contact with the organization. Dassault Systèmes and its SOLIDWORKS and DELMIAWorks teams are proud to be a small part of the SIGN story. To learn more about the non-profit and its mission, visit the SIGN Fracture Care International.
DELMIAWorks Additional Resources
Resource Center
Access brochures, case studies, testimonial videos, whitepapers, eSeminars (Webinars On-Demand), and more.
DELMIAWorks User Community
Online community of DELMIAWorks users (3DEXPERIENCE Platform login credentials required)
Training & Services
Learn more about DELMIAWorks Software Training Programs and Solution Consulting Services.
Have questions about DELMIAWorks Manufacturing ERP Solutions?
DELMIAWorks solutions solve your manufacturing challenges by connecting the entire design to manufacture process.