India has the world's fifth highest reserves of iron ore, making the country a strong competitor in the global steel industry. India's finished steel consumption, anticipated to increase by 230 million tons, has spurred innovation in steel processing. At the heart of steel processing are cold rolling mills that shape steel into ideal forms for manufacturing.
A leading flat steel processing equipment manufacturer in Faridabad, India (just south of Delhi), Yogiji Digi is saving energy with its sustainable innovations. For example, the company’s cold rolling mill designs have resulted in a 2 to 3 percent reduction in rolling power consumption. Additionally, it reduces CO2 emissions by 356 tons of every year.
"We have always focused on energy conservation and the environmental impact of the equipment we develop," says Managing Director Navneet Gill. "Most steel production mills use lots of water in the process. We have designed our mills to use less water compared to other mills. Every year, we save around 3.2 million liters of water [about 845,350 gallons] on each mill."
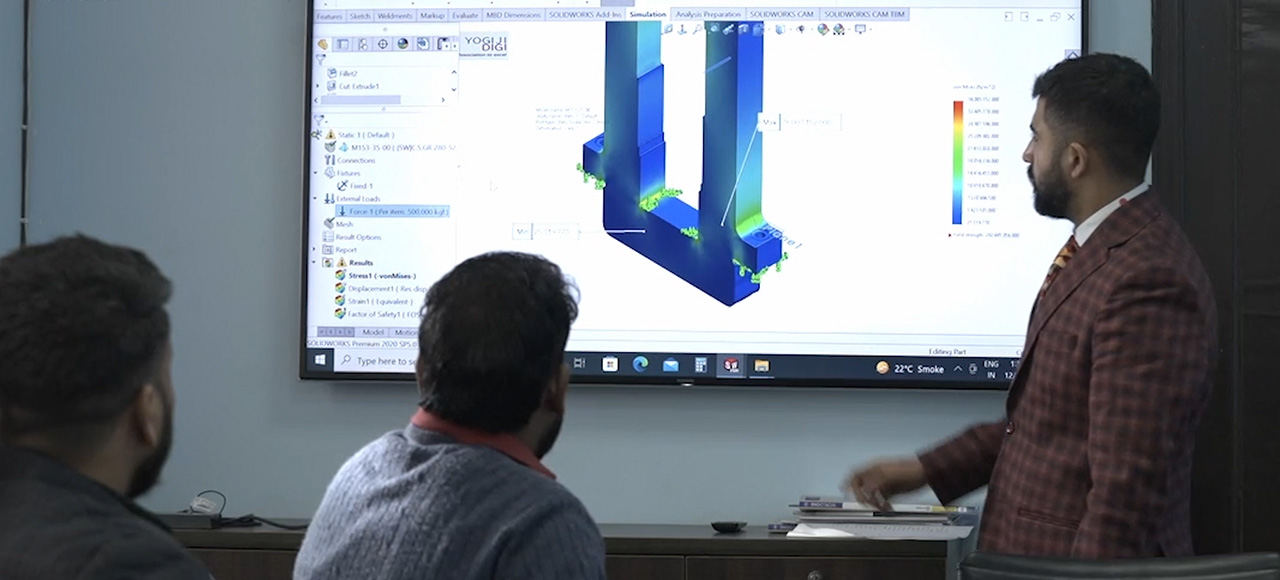
OPTIMIZED INDUSTRIAL MACHINERY DESIGN
One of the biggest challenges Yogiji Digi faces is the sheer size and complexity of its flat steel processing equipment. “It takes lots of time to build the equipment from scratch," according to Navneet. "We have been able to overcome this challenge using the SOLIDWORKS Simulation platform.
High-speed rolling mill design demands accuracy and precision within microns. "There's no scope for error," says Head of Project Management Aseem Gill. "The design needs to be absolutely perfect." Due to size alone, most industrial machinery contains a staggering number of mechanical and electrical components. "SOLIDWORKS has made life a lot easier," emphasizes Aseem. "Generating the bill of materials used to take me two days. With SOLIDWORKS, it takes just two hours."
Yogiji Digi also leverages SOLIDWORKS to improve the designs of its behemoth machinery. "We designed the mill housing and complete cold rolling mill assembly for one of our customers," explains Chief Operating Officer Varun Rana. "It ultimately helped us reduce the mill housing weight by up to 30 percent."
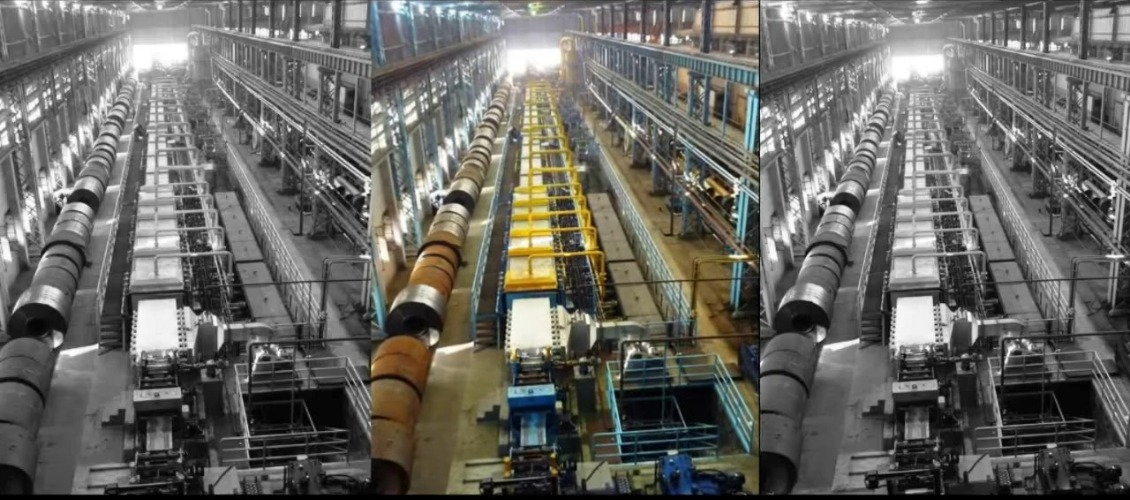